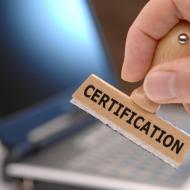
Наплавка. Плазменная наплавка – эффективный способ защиты металлических деталей Полуавтоматическая и автоматическая дуговая наплавка
Широкое применение в настоящее время находят плазменные способы наплавки. При плазменной наплавке (ПН) в качестве источника нагрева используется плазма, которая представляет собой вещество в сильно ионизированном состоянии. В 1 см 3 плазмы содержится 10 9 – 10 10 и более заряженных частиц. Практически в любом дуговом разряде образуется плазма. Основным методом получения плазмы для технологических целей является пропускание газовой струи через электрическую дугу, расположенную в узком медном канале. При этом в связи с отсутствием возможности расширения столба дуги возрастает число упругих и неупругих соударений заряженных частиц, т. е. увеличивается степень ионизации, возрастает плотность и напряжение дуги, что вызывает повышение температуры до 10000 – 15 000 о С.
Наличие у плазменных горелок стабилизирующего водоохлаждаемого канала сопла является основным отличием от обычных горелок, применяемых при сварке в среде защитных газов неплавящимся электродом.
При упрочнении и восстановлении деталей в зависимости от их формы, условий работы применяют несколько разновидностей плазменной наплавки, отличающихся типом присадочного металла, способом его подачи на упрочняемую поверхность и электрическими схемами подключения плазмотрона.
При плазменной наплавке по отношению к наплавляемой детали применяют два вида сжатой дуги: прямого и косвенного действия. В обоих случаях зажигание дуги плазмотрона и осуществление процесса наплавки выполняют комбинированным способом: вначале между анодом и катодом плазмотрона с помощью осциллятора возбуждают дугу косвенного действия.
Дуга прямого действия образуется при соприкосновении малоамперной (40 – 60 А) косвенной дуги с токоведущей деталью. В зону дуги могут подаваться материалы: нейтральная или токоведущая проволока, две проволоки (рис. 8.8), порошок, порошок одновременно с проволокой.
Метод косвенной дуги заключается в том, что между дежурной дугой и токоведущей проволокой образуется прямая дуга, продолжение которой является косвенной независимой дугой по отношению к электрически нейтральной детали.
Высокую производительность (до 30 кг/ч) обеспечивает плазменная наплавка с подачей в ванну двух плавящихся электродов 1 (рис.8.8), подключенных последовательно к источнику питания и нагреваемых почти до температуры плавления. Защитный газ подается через сопло 2.
Универсальный способ плазменной наплавки – наплавка с вдуванием порошка в дугу (рис.8.9). Горелка имеет три сопла: 3 – для формирования плазменной струи, 4 – для подачи присадочного порошка, 5 – для подачи защитного газа. Один источник тока служит для зажигания дуги осциллятором 2 между электродом и соплом, а другой источник тока формирует плазменную дугу прямого действия, которая оплавляет поверхность изделия и плавит порошок, подающийся из бункера 6 потоком газа. Изменяя ток обеих дуг устройствами 1, можно регулировать количество теплоты, идущей на плавление основного металла и присадочого порошка и, следовательно, долю металла в наплавленном слое.
Рис. 8.9 . Плазменная порошковая наплавка
Увеличение производительности процесса плазменной наплавки во многом зависит от эффективности нагрева порошка в дуге. Температура, которую приобретают частицы порошка в дуге, определяется интенсивностью и продолжительностью нагрева, зависящими от параметров плазмы, условия ввода порошка в дугу, технических параметров процесса наплавки. Наибольшее влияние на нагрев порошка оказывают ток дуги, размер частиц и расстояние между плазмотроном и анодом.
Основные достоинства метода ПН: высокое качество наплавленного металла; малая глубина проплавления основного металла при высокой прочности сцепления; возможность наплавки тонких слоев; высокая культура производства.
Основные недостатки ПН: относительно невысокая производительность; необходимость в сложном оборудовании.
Плазменная наплавка – это современный метод наложения износоустойчивого покрытия на рабочую поверхность. Он применяется при производстве и восстановлении изношенных машинных деталей. В современной технологии сварки этот метод занял важное место.
Где применяют эту технологию
Ее используют для наделения рабочей поверхности такими свойствами:
- антифрикционность;
- жароустойчивость;
- кислотоупорность;
- устойчивость к коррозии;
- устойчивость к износу.
При помощи плазменной наплавки получаются разные изделия:
- зубцы для ковша экскаватора;
- вкладыши на подпятники для габаритного турбогенератора;;
- поршни;
- подшипники и др.
В конструкциях из металла, произведенных способом наплавления, выходит сварочное соединение разных металлов. Характеристики таких изделий напрямую зависимы от показателя глубины проплавки основы, от перемещения элементов из металла-основы в состав наплавки. При таком соединении образуются новые фазы и составляющие структуры, которых не было в основе и материале-присадке.
Выпуск высокопрочных изделий – это дорогостоящий процесс. Поэтому, финансово выгодно выпускать их из достаточно прочного металла, а затем наложить защитное покрытие.
Суть применения
Она совсем не сложная. Для покрытия используют материал из проволоки или мелкий порошок в гранулах. Попадая в струю плазмы, он греется, а после плавится. В таком состоянии материал-защита подается на деталь. Одновременно с этим процессом непрерывно нагревают и саму деталь.
Преимущества данной технологии:
- Поток плазмы дает возможность наложить материалы, которые отличаются по своим параметрам. Выполнить это можно в несколько слоев. Таким образом, металл покрывают разными покрытиями с индивидуальными защитными особенностями.
- Широкие границы регулирования энергетических возможностей плазменной дуги, потому, что она является наиболее гибким источником тепла.
- Плазменный поток имеет очень высокую температуру, из-за чего он плавит тугоплавкие материалы.
- Формы и размеры детали для наплавления не снижают показатели технических характеристик данного метода. Также при этом не снижается показатель результата.
Если сравнить эту технологию с электродуговой сваркой, то плазменная наплавка имеет значительное преимущество:
- Металл перемешивается по минимуму.
- Минимальные тепловые затраты.
- Абсолютный контроль дуги.
- Полученное покрытие гладкое при небольшой механической обработке.
- Чистота наплавленных слоев.
- Цельное покрытие без пор.
- Высокий показатель прочности соединения.
Технология метода и его особенности
Наплавка металла по описываемой технологии производиться двумя методами:
- В струю вводят проволоку, ленту, или прут (они являются присадочным материалом).
- В струю подают смесь из порошка. Она смещается на поверхность металла газом.
Струя плазмы по компоновке разделяется на такие виды:
- закрытая;
- открытая;
- комбинированный вариант.
Из газов для создания огня используется:
- кислород;
- водород;
- аргон;
- гелий.
Профессионалы отдают предпочтение аргону и гелию.
Установки для этого вида наплавки
Для этого процесса применяют различные установки, их вид зависит от объемов производства, от требований к уровню автоматики. Соответственно этим потребностям выполнены универсальные и специализированные установки. Универсальное оборудование позволяет выполнять наплавку на деталях разной формы. Специализированные установки предназначены для деталей одного вида (например: клапаны для моторов внутреннего сгорания, для дисков, элементов-соединений бурильных труб и так далее).
Все эти установки оснащают новейшими системами управления с применением промышленных компьютеров. Это в значительной мере поднимает качество, стабильность и надежность работы.
Каждая установка отвечает требованиям современности по экобезопасности. В них установлены автономные блоки охлаждения водяным путем и камеры-защиты. Эта камера отлично защищает мастера от вредного влияния излучения плазменной дуги и от газов и пыли, которая выделяются при наплавке.
Плазменная наплавка зарекомендовала себя, как успешная новейшая технология, которая отличается высоким показателем качества. Она снижает затраты на ремонт больших агрегатов. Рабочие поверхности изделий после обработки становятся износоустойчивыми, жаропрочными, кислоупорными. Данный метод, благодаря широкому ряду технических характеристик, нашел широкое применение в разных областях.
Одним из основных методов повышения надежности и ресурса стеклоформ, клапанов, запорной арматуры является плазменная наплавка (Plasma transfer Arc, PTA).
Использование метода плазменно-порошковой наплавки позволяет существенно повысить качество наплавляемых деталей, увеличить производительность и придать особые свойства наплавляемой поверхности.
Выбор в сторону метода PTA крупнейшими производителями и потребителями запорной арматуры, формокомплектов для производства стекла, клапанов - подтверждает выгоды использования метода плазменно-порошковой наплавки, поскольку получаемый наплавленный слой с повышенными свойствами позволяет существенно повысить сроки службы деталей и узлов, продлить межремонтные интервалы и сократить затраты на капитальный и текущий ремонт.
Установки плазменной наплавки KSK предназначены для наплавки деталей от колец и клапанов до чистовых стекольных форм и деталей запорной арматуры.
- Повышение конкурентоспособности: предлагаемые нами методы применяются всеми ведущими зарубежными производителями арматуры, стекла, клапанов, валков.
- Увеличение межремонтных циклов: срок эксплуатации деталей увеличивается от 3 до 10 раз.
- Сокращение простоев: уменьшение количества остановок, и, соответственно, меньше времени на отладку оборудования для выхода на нужный режим.
Профессиональное оборудование для наплавки
Компания ООО «Метсол» представляет вниманию потенциальных заказчиков автоматические установки плазменной наплавки от чешского производителя KSK. Оборудование предназначено для проведения наплавки уплотнительных и рабочих поверхностей, включая стеклоформы, седла запорно-регулирующей арматуры, кольца клапана, наплавки внутренних диаметров. Конструкция плазмотронов подходит для изделий различной формы и способов наплавки. Разработчики предлагают 7 типов плазматронов, гарантирующих даже при максимальном режиме работе эффективное охлаждение установки. В процессе работы допускается корректировка настроек сварочных программ оператором через сенсорный экран на панели пульта. Это позволяет уменьшить в тестовых образцах процент брака.
Качественный подход
Одним из направлений деятельности компании ООО «Метсол» является поставка, установка и наладка заказчикам установки плазменной наплавки в Екатеринбурге. Опытные специалисты эффективно решают производственные задачи на высоком профессиональном уровне. Сервисная служба владеет современными знаниями в области сварочных технологий и металлообработки. Решив купить автоматическую установку плазменной наплавки вы получите:
- Повышение конкурентоспособности на уровне ведущих зарубежных производителей арматуры, стекла, клапанов, валков.
- Увеличение межремонтных интервалов: срок эксплуатации деталей увеличивается от 3 до 10 раз.
- Сокращение простоев и количества остановок.
Технология
Плазменно-порошковая наплавка износостойких материалов на заводе в г. Щербинка
Плазмой называется высокотемпературный сильно ионизированный газ, состоящий из молекул, атомов, ионов, электронов, световых квантов и др. При дуговой ионизации газ пропускают через канал и создают дуговой разряд, тепловое влияние которого ионизирует газ, а электрическое поле создает направленную плазменную струю. Газ может ионизироваться также под действием электрического поля высокой частоты. Газ подается при давлении в 2 …3 атмосферы, возбуждается электрическая дуга силой 400 … 500 А и напряжением 120 … 160 В Ионизированный газ достигает температуры 10 … 18 тыс. С, а скорость потока - до 15000 м/сек. Плазменная струя образуется в специальных горелках - плазмотронах . Катодом является неплавящий вольфрамовый электрод.
В зависимости от компоновки различают:
- Открытую плазменную струю (анодом является деталь или пруток). В этом случае происходит повышенный нагрев детали. Используется эта схема для резки металла и для нанесения покрытий.
- Закрытую плазменную струю (анодом является сопло или канал горелки). Хотя температура сжатой дуги на 20 …30% в этом случае выше, но интенсивность потока ниже, т. к. увеличивается теплоотдача в окружающую среду. Схема используется для закалки, металлизации и напыления порошков.
- Комбинированная схема (анод подключается к детали и к соплу горелки). В этом случае горят две дуги. Схема используется при наплавке порошком.
Плазменную наплавку металла можно реализовать двумя способами:
- Струя газа захватывает и подает порошок на поверхность детали;
- В плазменную струю вводится присадочный материал в виде проволоки, прутка, ленты.
В качестве плазмообразующих газов можно использовать аргон , гелий , азот , кислород , водород и воздух . Наилучшие результаты наплавки получаются с аргоном и гелием.
Достоинствами плазменной наплавки являются:
- Высокая концентрация тепловой мощности и минимальная ширина зоны термического влияния.
- Возможность получения толщины наплавляемого слоя от 0,1 мм до нескольких миллиметров.
- Возможность наплавления различных износостойких материалов (медь, латунь, пластмасса) на стальную деталь.
- Возможность выполнения плазменной закалки поверхности детали.
- Относительно высокий КПД дуги (0.2 …0.45).
- Малое (по сравнению с другими видами наплавки) перемешивание наплавляемого материала с основой, что позволяет достичь необходимых характеристик покрытий.
Поверхность детали необходимо готовить к наплавке более тщательно, чем при обычной электродуговой или газовой сварке, т. к. посторонние включения уменьшают прочность наплавленного слоя. Для этого производится механическая обработка поверхности (проточка, шлифование, пескоструйная обработка..), иногда обезжиривание. Мощность электрической дуги подбирают такой, чтобы сильно не нагревалась деталь, и чтобы основной металл был на грани расплавления.
Применение
Плазменная наплавка широко применяется для защиты от высокотемпературного износа формокомплектов стекольной промышленности, для защиты от коррозии и износа деталей запорной и запорно-регулирующей арматуры , для упрочнения поверхности деталей, работающих при высоких нагрузках.
Литература
- Хасуи А., Моригаки О. Наплавка и напыление. Пер. с яп. Москва « Машиностроение » 1985г.
Wikimedia Foundation . 2010 .
Плазменная наплавка является современным способом нанесения износостойких покрытий на рабочую поверхность при изготовлении и восстановления изношенных деталей машин. Плазмой называется высокотемпературный сильно ионизированный газ, состоящий из молекул, атомов, ионов, электронов, световых квантов и др.
При дуговой ионизации газ пропускают через канал и создают дуговой разряд, тепловое влияние которого ионизирует газ, а электрическое поле создает направленную плазменную струю. Газ может ионизироваться также под действием электрического поля высокой частоты. Газ подается при давлении в 2…3 атмосферы, возбуждается электрическая дуга силой 400…500 А и напряжением 120…160 В Ионизированный газ достигает температуры 10…18 тыс. °С, а скорость потока - до 15000 м/сек. Плазменная струя образуется в специальных горелках - плазмотронах . Катодом является неплавящий вольфрамовый электрод.
Схема плазменной наплавки открытой и закрытой плазменной струей.
В зависимости от компоновки различают:
- Открытую плазменную струю (анодом является деталь или пруток). В этом случае происходит повышенный нагрев детали. Используется эта схема для резки металла и для нанесения покрытий.
- Закрытую плазменную струю (анодом является сопло или канал горелки). Хотя температура сжатой дуги на 20 …30% в этом случае выше, но интенсивность потока ниже, т.к. увеличивается теплоотдача в окружающую среду. Схема используется для закалки, металлизации и *напыливания *порошков.
- Комбинированная схема (анод подключается к детали и к соплу горелки). В этом случае горят две дуги, Схема используется при наплавке порошком.
- струя газа захватывает и подает порошок на поверхность детали;
- в плазменную струю вводится присадочный материал в виде проволоки, прутка, ленты.В качестве плазмообразующих газов можно использовать аргон, гелий, азот, кислород, водород и воздух. Наилучшие результаты наплавки получаются с аргоном и гелием.
- Высокая концентрация тепловой мощности и минимальная ширина зоны термического влияния.
- Возможность получения толщины наплавляемого слоя от 0,1 мм до нескольких миллиметров.
- Возможность наплавления различных износостойких материалов (медь, латунь, пластмасса) на стальную деталь.
- Возможность выполнения плазменной закалки поверхности детали.
- Относительно высокий К. П. Д. Дуги (0.2 …0.45).
- Малое (по сравнению с другими видами наплавки) перемешивание наплавляемого материала с основой, что позволяет достичь необходимых характеристик покрытий.
Описание установки плазменной наплавки - .
Поверхность детали необходимо готовить к наплавке более тщательно чем при обычной электродуговой или газовой сварке, т.к. при этом соединение происходит без металлургического процесса, поэтому посторонние включения уменьшают прочность наплавленного слоя. Для этого производится механическая обработка поверхности (проточка, шлифование, пескоструйная обработка..) и обезжиривание. Мощность электрической дуги подбирают такой, чтобы сильно не нагревалась деталь, и чтобы основной металл был на грани расплавления.
Плазменная наплавка широко применяется для защиты от высокотемпературного износа формокомплектов стекольной промышленности, для защиты от коррозии и износа деталей запорной и запорно-регулирующей арматуры, для упрочнения поверхности деталей, работающих при высоких нагрузках.